XR-5 was chosen as a more long term cost effective alternative to concrete, asphalt or unreinforced geomembranes to line the containment area around fuel storage tanks at Pearl Harbor.
Project Details: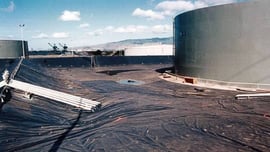
Name: Pearl Harbor Fuel Storage Tanks
Dates: Installed in 1995
Location: Pearl Harbor, HI
Project Story:
As a major supply point for the U.S. Military, fuel storage at Pearl Harbor has long been critical to operations in the Pacific. As ships transitioned to fuel oil in the 1920’s, large scale tank fuel storage was first constructed there.
Several facilities were constructed during that time, with the Upper Tank Farm having the largest tanks, the largest ever built at Pearl Harbor. There were 17 tanks, 40 ft (12 m) tall, 164 ft (50 m) diameter, holding 150,000 barrels (6.3 million gallons, 24,000 m3) each. That facility remains today and has been continually upgraded and provided with state-of-the-art fuel spill containment geomembranes, up to as recently as 2020.
Figure 1: Upper Tank Farm, Circa 1926
Source: Department of the Navy, Bureau of Yards and Docks
Beginning in early 1942, the tanks at the Upper Tank farm were retrofitted with various upgrades including portable foam systems and there was “placed a six-inch clay layer throughout the berms in order to prevent oil leakage into the harbor and the resulting fire hazard”, representing an early effort at creating an impervious surface, or layer. During and after WW II, with the massive Red Hill Underground storage facility operational, the size of the Upper Tank farm was decreased such that by 1959, only 6 tanks of the original 17 remained. These large tanks at the Upper Tank Farm, then and even now, represent the only substantive alternative fuel storage for the fleet and Pearl Harbor activities, to the Red Hill tanks. (Note: In March 2022, the Department of Defense announced that the Red Hill facility would be shut down due to leaking fuel contaminating drinking water in the area. The tanks are to be defueled and taken offline with final closure in place by 2027.)
By the late 1990’s, 5 of the original tanks of the 1924 construction remained (with many upgrades) over the years. The 6th tank burned in 1978 and was rebuilt at the same location. The other aboveground fuel storage facilities throughout Pearl Harbor have also been essentially decommissioned.
Complying with Oil Spill Control Regulations
In October 1978, President Carter signed Executive Order 12088 which required all Federal facilities to comply with pollution control standards. 40 CFR 112 which regulated spill prevention activities was published in 1973, under authority granted by the Clean Water Act of 1972. Subsequent to Executive Order (Naval Executive Order in the case of Pearl Harbor) 12088, all Federal facilities began taking inventory of where facilities would be out of compliance. This is much the same as was also happening in the private sector.
The oil storage facilities had a history of petroleum releases and began enacting various improvements over the next decade. Included was a design by the Naval Facilities Engineering Command-Pacific Division (NAVFAC PACDIV) to provide “sufficiently impervious” surfaces for the bermed areas at the remaining aboveground fuel storage areas including the Upper Tank Farm, Pearl City Annex and some at Red Hill. The Federal Oil spill containment regulations (40 CFR 112) required spills be contained by surfaces with impervious characteristics, impervious to the stored product. The containment design called for the construction of a 3” (7.5 cm) thick reinforced concrete liner in the flat areas (including water stops) with a spray Gunite layer on the containment slopes. Access roads into and within the bermed areas were to be 6” (15 cm) reinforced concrete. At 35% design, it was decided to verify the appropriate technology and look for cost savings. PACDIV Commissioned a VE study to U.S. Cost Inc.
The identified alternate technologies to the reinforced concrete/spray Gunite for secondary containment that were identified, and cost evaluated where:
- 2” (5 cm) asphalt with fuel resistant sealant 3” (7.5 cm), for roads
- Buried 80 mil (2.0 mm) fuel resistant non reinforced geomembrane
- Buried 30 mil (0.75 mm) fuel resistant reinforced geomembrane
- Bentonite mats
- Exposed 30 mil (0.75 mm) fuel resistant reinforced geomembrane
- Spay-applied polyamid
- Reinforced concrete with 30 mil (0.75 mm) fuel resistant geomembrane on slopes
Prepared aggregate bases for the non-geomembrane options were provided. Geotextile protection was to be provided for the geomembrane options. Total area considered was 780,000 ft2 (72,500 m2).
Net life cycle cost saving ranged from -$254,326 (Spray applied polyamid) to $1,748,656 (exposed 30 mil (0.75 mm) fuel resistant reinforced geomembrane on the floor and slopes). The base cost for the concrete/Gunite was $3.52M with a total system cost of $5.337M. To equal these to today’s (2024) dollars, all these costs can essentially be increased by a factor of 2.3.
For life cycle costing, a 25-year period was used. It is interesting to note the assumptions used in the cost evaluation, for maintenance and life span of each option:
Containment Option | Maintenance Requirements | Replacement Cycle |
3” (7.5 cm) Reinforced Concrete (Base Option) |
Yearly Joint/crack repair |
25 years |
Buried 80 mil (2.0 mm) non reinforced Fuel Resistant Geomembrane |
No Maintenance |
Replace at 20 yr. |
Buried 30 mil (0.75 mm) reinforced fuel Resistant Geomembrane |
No Maintenance |
Replace at 20 yr. |
Bentonite Mats (Floor) |
No Maintenance |
25 years |
Exposed 30 mil (0.75 mm) Fuel Resistant reinforced Geomembrane |
Annual cleaning, minor repairs |
Replace every 12 years |
Spray applied Polyamid |
No Maintenance |
Replace at 20 yr. |
Reinforced concrete with Exposed 30 mil (0.75 mm) Fuel Resistant Geomembrane on slopes |
Annual cleaning, minor repairs |
Same as concrete and as Exposed 30 mil (0.75 mm) Fuel Resistant Geomembrane |
Figure 2: VE Study Containment Options
One can argue with the assumptions, but the cost analysis comparisons were performed using these criteria.
The Exposed 30 mil (0.75 mm) Fuel Resistant reinforced Geomembrane offered the greatest life cycle savings for many reasons, even though it had the shortest assumed life span. How can that be? Look at these contributing factors to the individual candidates:
- Asphalt had high recurring maintenance costs.
- The buried 80 mil (2.0 mm) non-reinforced geomembrane had high installation costs and added costs for over excavation to accommodate overburden along with drainage modifications, and the overburden itself.
- The buried 30 mil (0.75 mm) reinforced geomembrane had higher costs due to over excavation to accommodate overburden along with drainage modifications and the overburden itself.
- The Bentonite mats and spray applied polyamid had remarkably high initial costs.
It should also be noted that all the alternatives were considered equal in the ability to hold any spilled oil whether short term or long term. There are in fact, substantial differences between the materials in long term chemical resistance and permeability. On the other hand, it was realized even in 1991 that unreinforced, crystalline products like polyethylene require protective cover. It was also realized the fuel resistant reinforced product would require heavy internal reinforcing fabric to be comparable to the other alternatives.
The VE study recommended the use of an exposed 30 mil (0.75 mm) reinforced fuel resistance, geomembrane with replacement on a 12-year cycle.
Installation of Geomembrane at the Upper Tank Farm
In 1995, Seaman Corporation's XR-5 geomembrane was installed at the above ground fuel storage facilities which included the Upper Tank Farm.
Figures 3-5. 1995 XR-5 Geomembrane installation at Upper Tank Farm. Note geomembrane over interior slopes. Photo 1996. Source: Seaman Corporation
The XR-5 was brought completely over all internal berms rather than terminating with batten bars at the top of the slopes. PACDIV’s design retained and upgraded the internal roads, which primarily eliminated or reduced need for access via the slopes. The road design retained the cross section in the original base design, which was 6” (15 cm) of concrete over a prepared base. The geomembrane was terminated and anchored at the edge of the road. These roads are substantial due to the size of the tanks and the potential maintenance activities. The drainage was to oil water separators.
The Upper Tank Farm lives on to a new century
Between 1995 and 2020, virtually all of the above ground storage, except the Upper Tank Farm was decommissioned. After 12 years of service, the geomembrane was still in excellent condition and was not replaced.
In 2019, PACDIV indicated their intentions to use appropriated funds (per the VE study in 1991) to replace the geomembrane at the Upper Tank Farm. There was no indication of deterioration to the material. To establish a quantitative base line on the condition of the material at that point, field samples were acquired for thickness measurement, as an indicator of the effect of 24 years of sunlight exposure in Hawaii. Figure 6 illustrates the microscopic cross section of the exposed sample taken from the Upper Tank Farm original 1995 installation.
Figure 6. 50X Microscopic cross section, 8130 XR-5 from Upper Tank Farm. Installed 1995, sample taken 2019.
Source: Seaman Corporation
The photo shows the thickness of the polymer over the base fabric, on the left and the overall thickness (27.9 mils, 0.70 mm) on the right. The original specification was 30 mils (0.75 mm). Based on this testing and reports from the field indicating polymer coating condition, Seaman Corporation did not recommend replacing the XR-5. However, due to the availability of appropriated funds and approaching the end of the 24-year design life cycle, PACDIV elected to replace the XR-5 at the Upper Tank Farm, with the same material and design.
The design of the geomembrane system was remarkably similar to that in the mid 1990’s. The XR-5 was factory fabricated into large panels to minimize field seaming, construction, quality assurance, installation delays and to provide maximize assurance of performance. The low thermal-expansion contraction rate of the geomembrane allowed an exposed installation, thus providing minimal maintenance and no concerns with overburden management, and ultimate disposal. Because the existing XR-5 still retained its original properties, it was left in place and the new XR-5 was installed over it.
Figure 7. Upper Tank Farm 2020
Source: Weston Associates
Figure 8. XR-5 over interior slope, 2020 Installation
Source: Layfield USA
For nearly 100 years, the Upper Tank Farm has provided fuel storage for the U.S. Navy’s Pacific Fleet. For the last quarter century and for years to come, the XR-5 Geomembrane has and will provide proven secure containment against spills or leaks at the facility.